PepsiCo, a global powerhouse in the food and beverage industry, stands as one of the world’s leading and diversified companies. Founded in 1965 through the merger of Pepsi-Cola and Frito-Lay, the company has evolved into a dynamic entity with a robust portfolio encompassing iconic beverage brands like Pepsi, Mountain Dew, and Gatorade, as well as popular snack brands such as Lay’s and Doritos. With a presence in numerous markets worldwide, PepsiCo has solidified its industry position by consistently delivering a diverse range of products that cater to evolving consumer tastes.
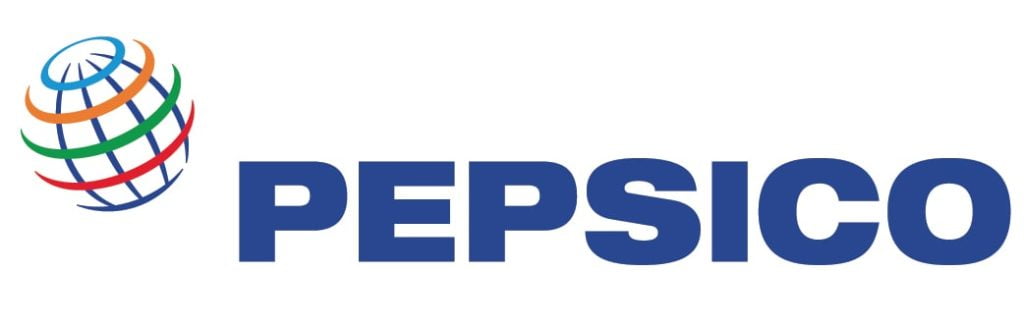
In this case study we will delve into understanding the ERP implementation process of PepsiCo, its why and why nots.
Rationale for Implementing Oracle ERP
PepsiCo’s global reach, innovative product offerings, and commitment to corporate responsibility underscore its influential position in the ever-evolving food and beverage sector.
The decision for PepsiCo to implement Oracle ERP in Financials and Supply Chain stems from a strategic need to enhance operational efficiency and adapt to the evolving demands of a dynamic business environment. With the continuous growth and expansion of PepsiCo’s global footprint, there arose a pressing necessity to streamline financial processes and fortify supply chain management.
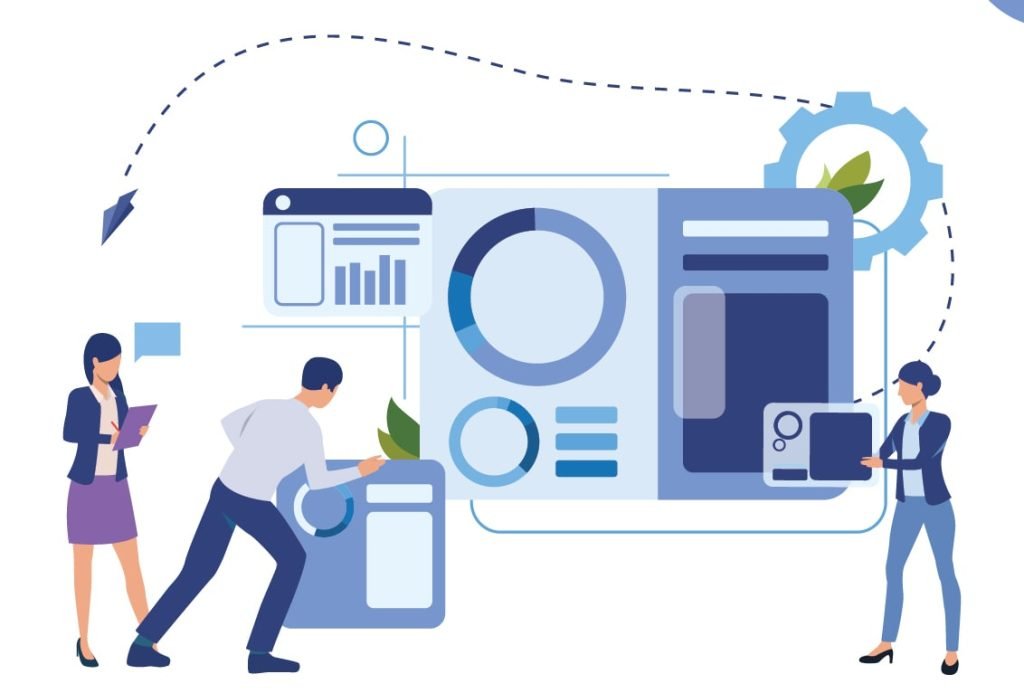
Oracle ERP, renowned for its comprehensive financial modules and robust supply chain capabilities, offered a tailored solution to address these specific needs. The integrated nature of Oracle ERP ensures seamless communication between financial and supply chain functions, providing real-time insights, optimizing inventory management, and fostering overall business agility. The scalability and flexibility of Oracle ERP align with PepsiCo’s vision for future growth, making it a strategic choice to navigate the complexities of modern business operations effectively.
The implementation of Oracle ERP in Financials and Supply Chain signifies a proactive approach by PepsiCo to leverage cutting-edge technology for sustained operational excellence and continued success in the competitive marketplace.
Why an Integrated ERP Solution
PepsiCo faced significant challenges in managing its financial processes and supply chain operations, primarily stemming from the sheer scale and complexity of its global operations. The existing systems struggled to provide real-time visibility into financial data, leading to delays in decision-making and potential inefficiencies in resource allocation. In the world of supply chain operations, managing inventory across diverse markets proved challenging, often resulting in suboptimal logistics and increased costs.
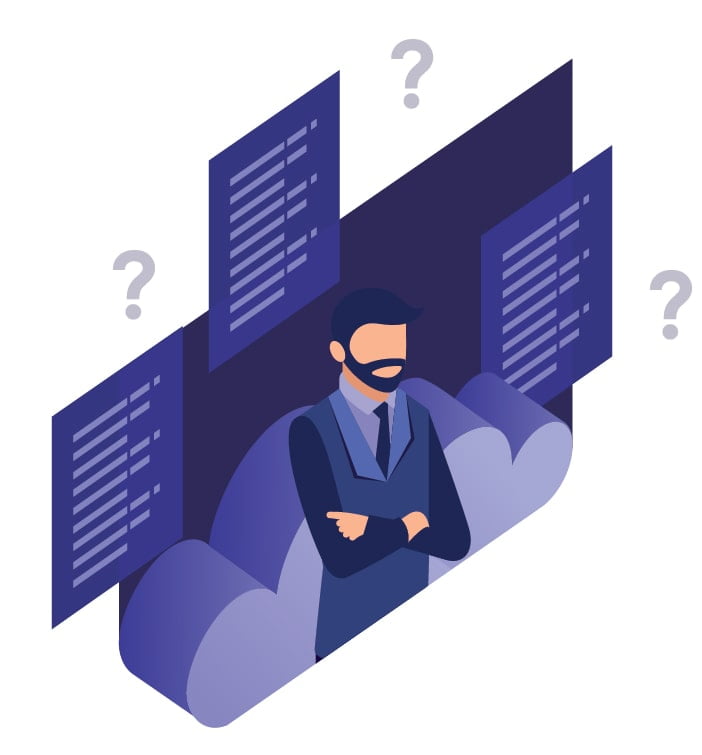
Recognizing the need for a cohesive and integrated solution, PepsiCo sought to implement an ERP system.
An integrated ERP solution, like Oracle ERP, was seen as essential to harmonize financial and supply chain functions, enabling streamlined processes, data visibility, and improved decision-making. The move towards an integrated ERP system reflects PepsiCo’s commitment to overcoming these challenges, fostering operational excellence, and ensuring the agility required to navigate the complexities of the food and beverage industry successfully.
Selecting the Right ERP
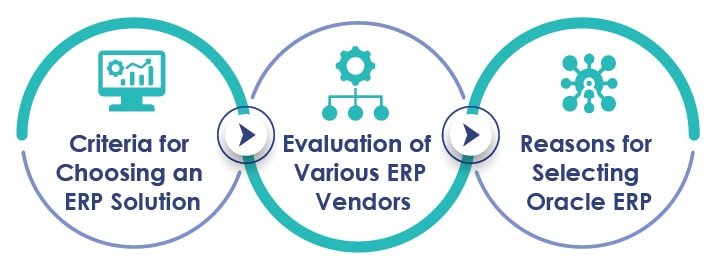
Criteria for Choosing an ERP Solution
- Comprehensive Functionality: PepsiCo sought an ERP solution that could seamlessly integrate financial and supply chain functions.
- Scalability: The chosen system needed to accommodate PepsiCo’s global expansion and evolving business requirements.
- Flexibility: The ERP had to adapt to the dynamic nature of the food and beverage industry.
- Cost-Effectiveness: Budget considerations played a crucial role in the selection process.
Evaluation of Various ERP Vendors
- PepsiCo conducted a thorough assessment of multiple ERP vendors, considering factors such as system capabilities, vendor reputation, and user feedback.
- In-depth analysis included the examination of features related to financial management, supply chain, scalability, and overall integration capabilities.
Reasons for Selecting Oracle ERP
- Comprehensive Financial Modules: Oracle ERP offered robust financial features crucial for PepsiCo’s complex financial operations.
- Supply Chain Management: The system’s strong supply chain capabilities aligned with PepsiCo’s goal to optimize inventory and enhance logistics.
- Scalability and Integration: Oracle ERP’s scalability and seamless integration capabilities made it the ideal choice for PepsiCo’s present needs and future growth.
Oracle ERP in Financials
Oracle ERP in Financials encompasses a suite of modules, including General Ledger, Accounts Payable, Accounts Receivable, and Fixed Assets. These modules work cohesively to manage financial transactions, track expenditures, and ensure accurate accounting.
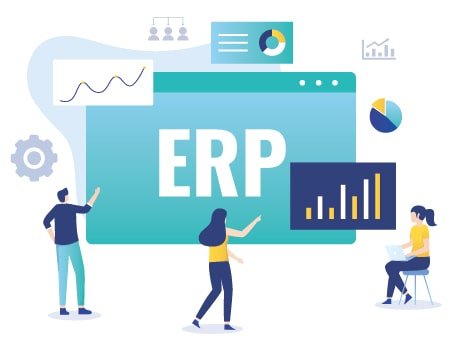
Improvements in Financial Reporting and Analysis
- Oracle ERP facilitates real-time financial reporting, providing stakeholders with immediate access to critical financial data.
- Advanced analytics tools within the system enhance the depth and accuracy of financial analysis, aiding in strategic decision-making.
Impact on Budgeting and Forecasting Processes
- The integration of Oracle ERP streamlines budgeting processes, allowing for more accurate forecasting and resource allocation.
- Improved budget visibility and control contribute to enhanced financial planning and management.
Oracle ERP in Supply Chain
Oracle ERP’s Supply Chain modules include Inventory Management, Order Management, and Procurement. These modules collaborate seamlessly to optimize supply chain processes from procurement to delivery.
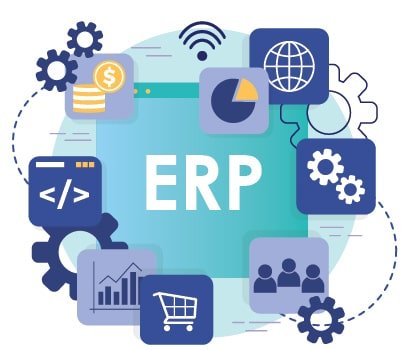
Enhancements in Inventory Management and Order Fulfillment
- Oracle ERP offers advanced inventory tracking and management features, minimizing excess inventory and improving stock turnover.
- Order fulfillment processes benefit from real-time data, reducing lead times and enhancing customer satisfaction.
Impact on Overall Supply Chain Efficiency
- The implementation of Oracle ERP in Supply Chain significantly improves the overall efficiency of supply chain operations.
- Enhanced visibility, coordination, and automation contribute to better decision-making, reduced operational costs, and increased agility in responding to market demands.
Integration and Collaboration
The integration and collaboration facilitated by Oracle ERP not only streamline operations but also pave the way for a more responsive and agile organizational structure, positioning the company for sustained growth and success.
How Oracle ERP Facilitated Integration Between Financial and Supply Chain Modules
- Oracle ERP acts as a unified platform, seamlessly integrating financial and supply chain modules.
- Shared databases and streamlined workflows ensure a cohesive flow of information between departments, fostering collaboration.
Collaboration Benefits Across Different Departments
- Oracle ERP promotes cross-departmental collaboration by providing a centralized data repository accessible to relevant teams.
- Financial and supply chain teams can collaborate more effectively, leading to improved coordination and a holistic view of organizational operations.
Key Benefits
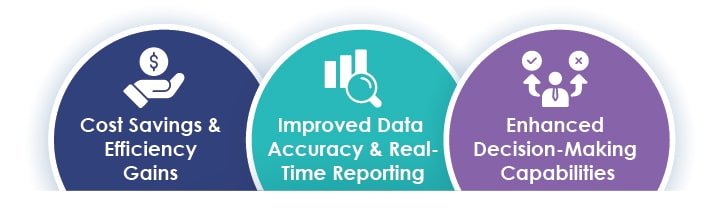
Cost Savings and Efficiency Gains
- The integration of financial and supply chain processes reduces manual effort and redundancy, leading to significant cost savings.
- Automation of routine tasks enhances overall operational efficiency, allowing resources to be allocated more strategically.
Improved Data Accuracy and Real-Time Reporting
- Oracle ERP ensures data consistency across financial and supply chain modules, minimizing errors.
- Real-time reporting capabilities empower stakeholders with accurate, up-to-date information, aiding in quicker and more informed decision-making.
Enhanced Decision-Making Capabilities
- With integrated data, decision-makers have a comprehensive understanding of the organization’s financial health and supply chain performance.
- Advanced analytics tools within Oracle ERP enable more informed decisions, contributing to long-term strategic planning and adaptability in a dynamic business environment.
Lessons Learnt for Future ERP Implementation
Implementing ERP systems offers valuable insights that contribute to the success of future implementations. Some key lessons learned include:
- Thorough Planning and Testing: Adequate planning and meticulous testing are critical to identify and address potential issues before full implementation.
- Strong Leadership and Project Management: Effective leadership and project management are vital for steering the implementation process, ensuring timely milestones, and addressing challenges promptly.
- Employee Involvement and Training: Involving employees early, addressing concerns, and providing comprehensive training programs are essential for successful user adoption and minimal resistance.
- Continuous Monitoring and Evaluation: Continuous monitoring and evaluation help identify areas for improvement, ensuring that the ERP system aligns with evolving business needs.
- Vendor Collaboration: Collaborating closely with the ERP vendor fosters a better understanding of system capabilities, potential upgrades, and ongoing support requirements.
- Change Management Strategies: Proactive change management strategies help ease the transition, mitigate resistance, and ensure a smooth adoption of new workflows and processes.
- Data Migration Considerations: Careful consideration of data migration processes is crucial to maintaining data accuracy and integrity during the transition to the new ERP system.
- Flexibility for Customization: Building flexibility into the ERP system for future customization allows the organization to adapt to changing business requirements.
- Communication: Clear and transparent communication at all stages of the implementation is essential for keeping stakeholders informed and aligned with the project’s goals.
- Post-Implementation Support: Establishing robust post-implementation support mechanisms ensures timely resolution of issues and ongoing system optimization.
Conclusion
PepsiCo’s strategic implementation of Oracle ERP in Financials and Supply Chain reflects a commitment to operational excellence and future growth. The integration of Oracle ERP streamlined processes, fostering collaboration and delivering key benefits such as cost savings, enhanced data accuracy, and improved decision-making. Lessons learned emphasize the importance of thorough planning, leadership, employee involvement, and continuous evaluation for successful ERP implementations. As PepsiCo continues to leverage cutting-edge technology, these insights will undoubtedly guide future implementations, ensuring sustained success in the competitive food and beverage industry.
Uncover impactful social media tactics to elevate audience interaction. Visit our website today to unleash the potential growth your brand deserves!
All images belong to their respective owners. Please email [email protected] if removal is required.